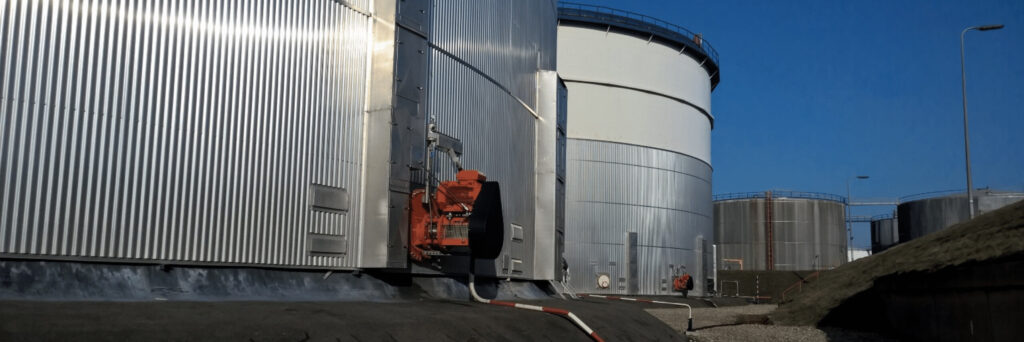
Petrochemical
The petrochemical industry starts often with the storage of crude oil, waiting to be refined and processed. With the storage of the crude oil customers have to deal with BS&W (Basic Sediment & Water), heat transfer and homogenization issues. Jongia engineers have developed side entry mixers for these applications based on CFD (Computational Fluid Dynamics) analysis and know-how, resulting in the most effective and efficient induced flow in the tank.
Jongia engineers are able to calculate on blending time and tank cycles for additives on fuel oils, kerosenes and diesels. Given the current global energy transition these types of fuels are getting more and more important for the industry as well as for the end users.
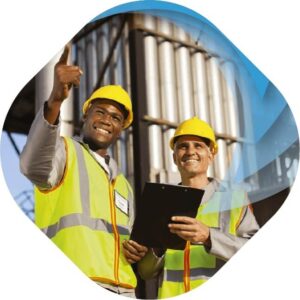
Maximum performance at minimum power input
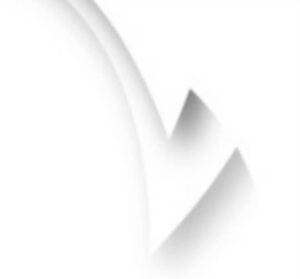
Further downstream where these products are being refined and processed to petrochemicals, Jongia has a lot of reference projects in monomers and polymers. From low viscous premix slurries to high viscous polymers in high pressure reactors, Jongia will design the most effective mixing element for best performance. Anchor type low speed mixing element will be challenged by a CRM geometry to gain the maximum output. In line dynamic mixing in Butyl-rubber process streams have been designed by our engineers for the most effective particle size (microns).
Jongia’s empiric know-how and theoretical knowledge results in the maximum performance and output of your process, based on the fact that we also make a cross reference on different technologies in another industry processes.
Applications
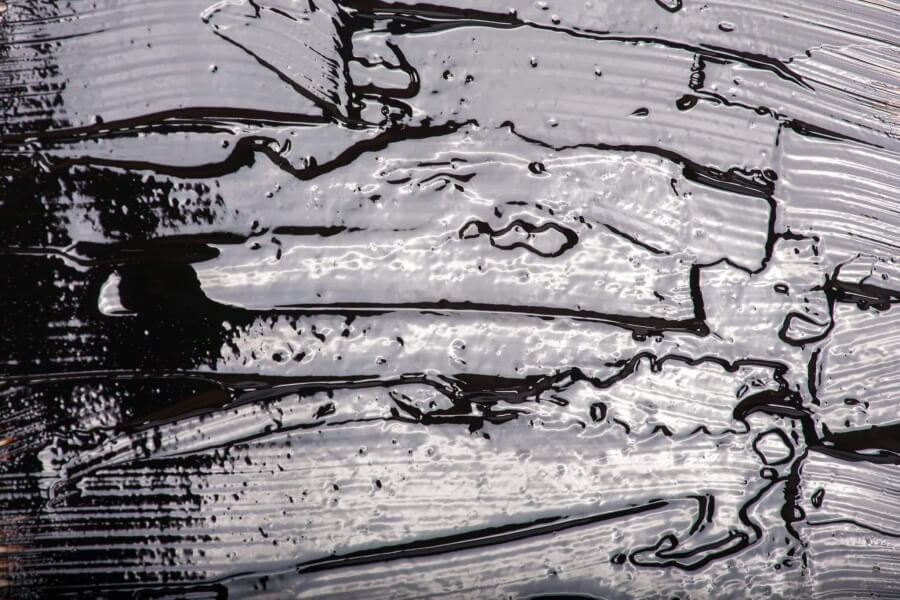
Crude oil
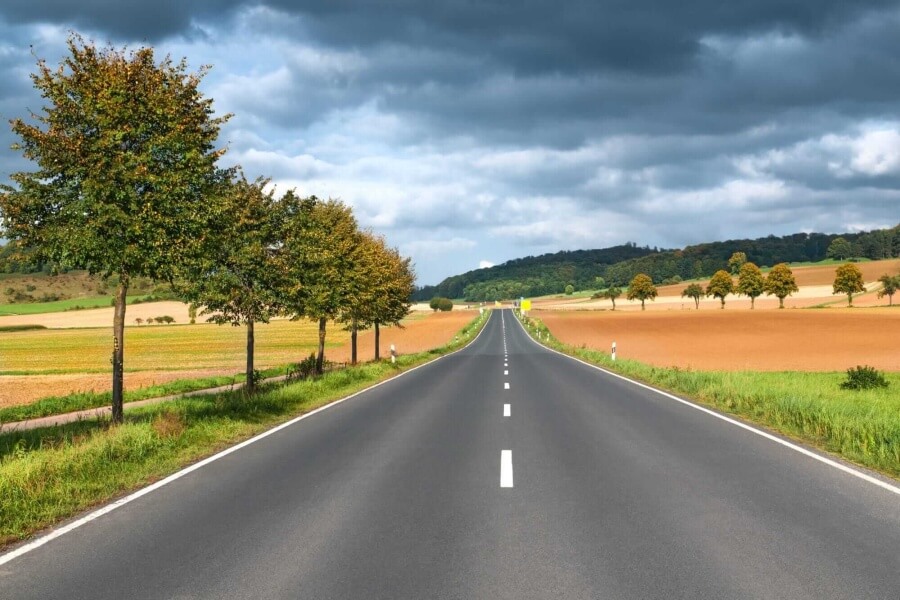
Bitumen
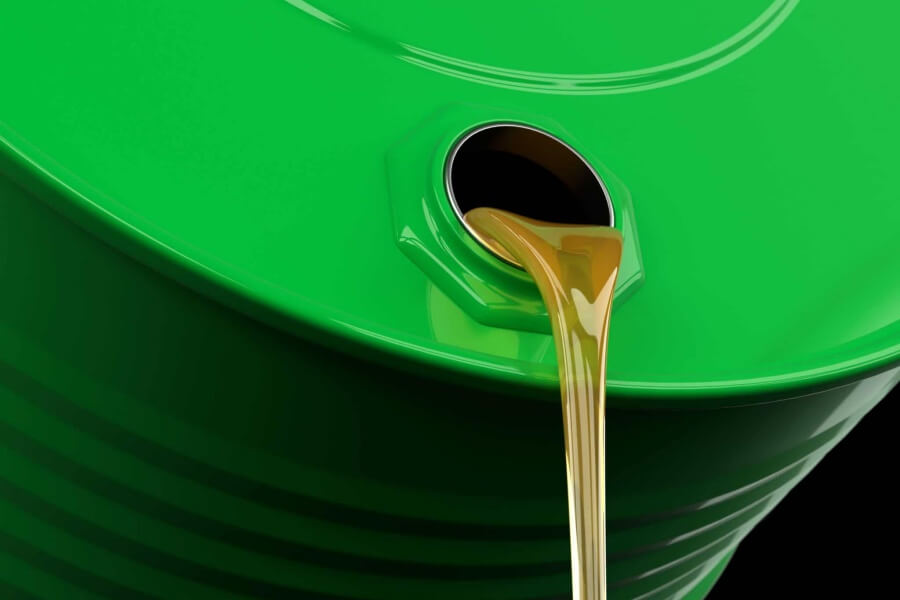
Fuel oil
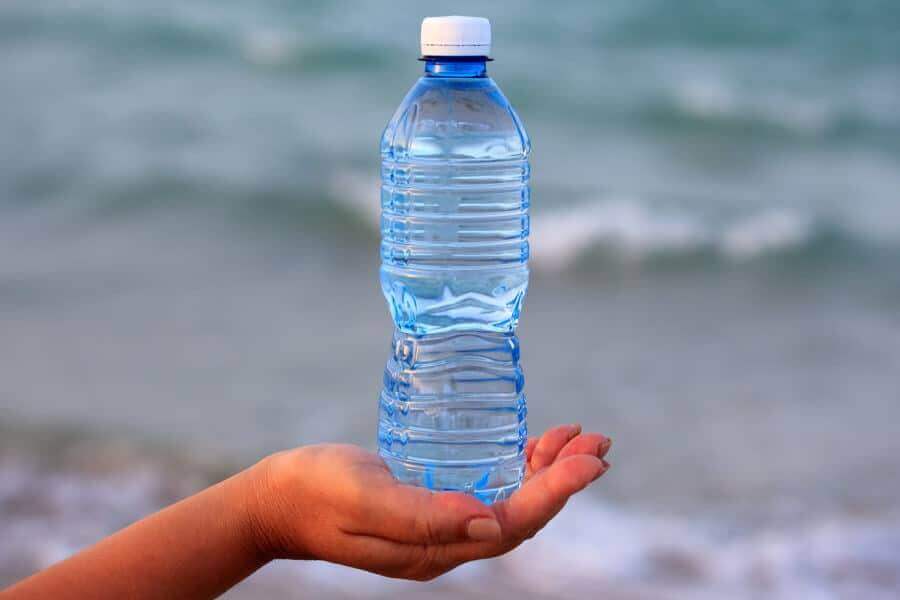
Plastics
Challenge us to improve your process
Other Chemical Industries
Frequently Asked Questions
What is the primary focus of the petrochemical industry?
The petrochemical industry primarily focuses on the storage and processing of crude oil, including managing issues like BS&W, heat transfer, and homogenization. Jongia engineers design efficient side entry mixers for optimal performance during these processes.
How do Jongia engineers enhance mixing efficiency?
Jongia engineers use Computational Fluid Dynamics (CFD) analysis to design mixers that achieve effective and efficient flow in storage tanks, ensuring a better blending process and addressing challenges in handling fuel oils, kerosenes, and diesels.
What are the applications of Jongia's mixing technology?
Jongia’s mixing technology is versatile, used in a range of applications from low-viscosity slurries to high-viscosity polymers in pressure reactors, optimizing the mixing process for various petrochemicals.
How do Jongia mixers contribute to fuel transitions?
With the global energy transition, Jongia mixers effectively enhance blending times and tank cycles for fuels, ensuring efficient processing of essential fuels like kerosenes and diesels, relevant for both industry and end users.
What benefits do Jongia's designs deliver?
Jongia’s designs, based on empirical know-how and theoretical principles, maximize performance and output in petrochemical processes, ensuring effective mixing solutions tailored to customer needs and specific production requirements.
Petrochemical – Related Articles
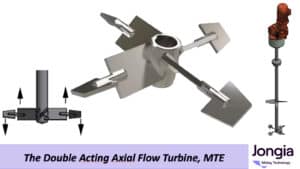
The Double Acting Axial Flow Turbine type AST-MTE mixing element
Operation of an AST-MTE Element Operation of an AST-MTE Element This element can be used in both CW (clockwise) and CCW (counterclockwise) directions. In one case, the inner AST element is downward-pumping with the outer tips pumping upward, and in
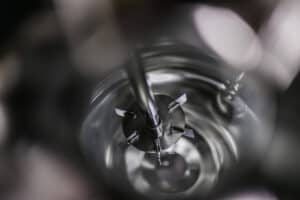
Jongia Mixing Technology Agitators in Process Installations
This reactor setup from Veenbrink RVS, equipped with Jongia agitators, forms the foundation for polymer production. The system is applied in an ATEX classified zone: the equipment zone 1 IIB T2, whilst the space itself is designated as zone 2

A New MD for Jongia Mixing Technology!
Leeuwarden, 23 April 2025 We are delighted to announce that we have a new Managing Director at Jongia Mixing Technology! Our new MD is Mr. Jean Philippe Pfeiffer. Jean Philippe has worked for De Dietrich for 29 years as Group