Jongia Mixing Technology recently delivered a series of agitators with Nord Maxxdrive gearboxes for the biogas plant of Brabant-based agricultural company Princepeel, part of the Smits Group. These ‘heavy duty’ Agitators optimally withstand the high torques required to move the liquid mass in the rectangular digestion bunkers.
From hunting grounds of the Princes of Orange to modern and sustainable livestock and arable farm: the Princepeel estate in the North Brabant town of Mill has undergone a remarkable transformation over the past centuries. Since the mid-1980s, it has been owned by the Smits family, whose third generation is now at the helm. The family business strives for long-term continuity, always investing and developing in sustainable business, without losing sight of the historical value of the estate. The business comprises ten pig farms and an arable farm dedicated to the cultivation of leeks, asparagus, flower bulbs, maize, sugar beet and raspberries, among others.
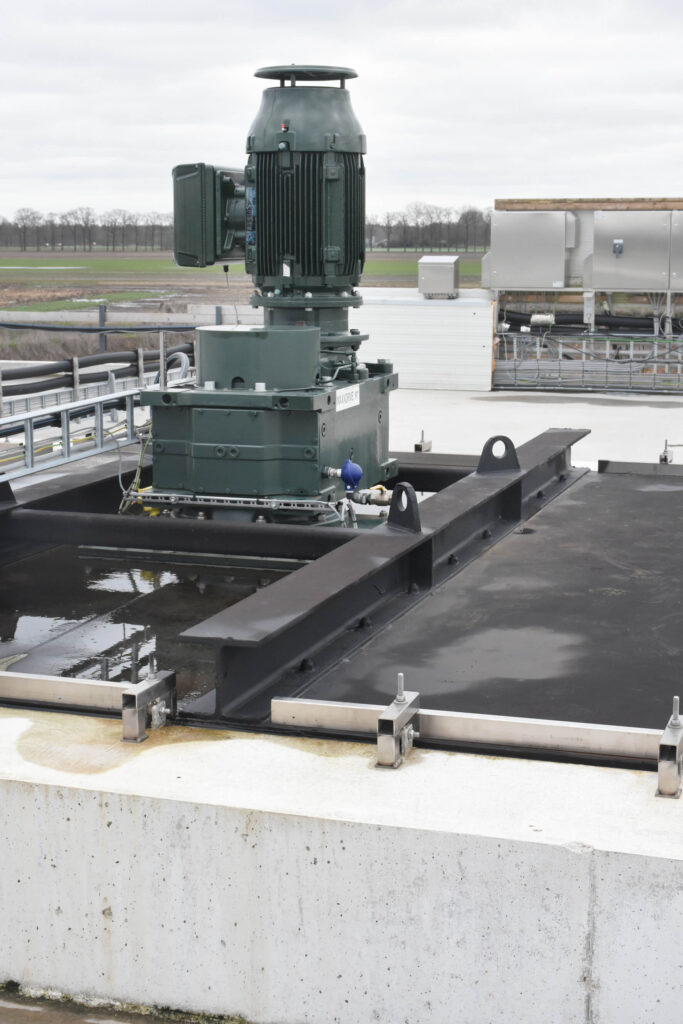
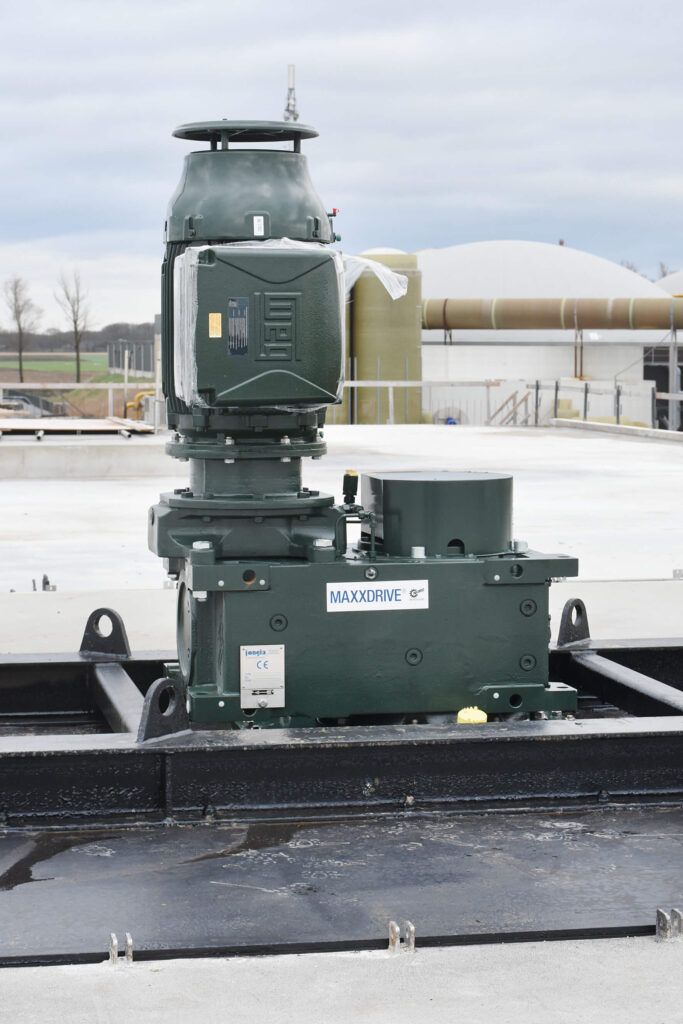
Circular
Director Pieter Smits: “We try to work completely circularly. In our digestion plant, we convert manure from the pigsties and farm residues into digestate, a residue from the digestion process, and biogas. This not only provides energy for our own farm, but also gas for some 12,500 households in the immediate vicinity. We also generate all the electricity for our own company. We partly use the digestate ourselves and partly sell it to third parties, including French winegrowers. This is because it is a good replacement for artificial fertiliser. On our own farm, we pump it through pipes to the fields, eliminating transport by tractor or truck. This is more sustainable and saves time and money.” Incidentally, the biogas plant processes not only its own residues, but also organic residues from the food industry through its sister company KwaliFlex.
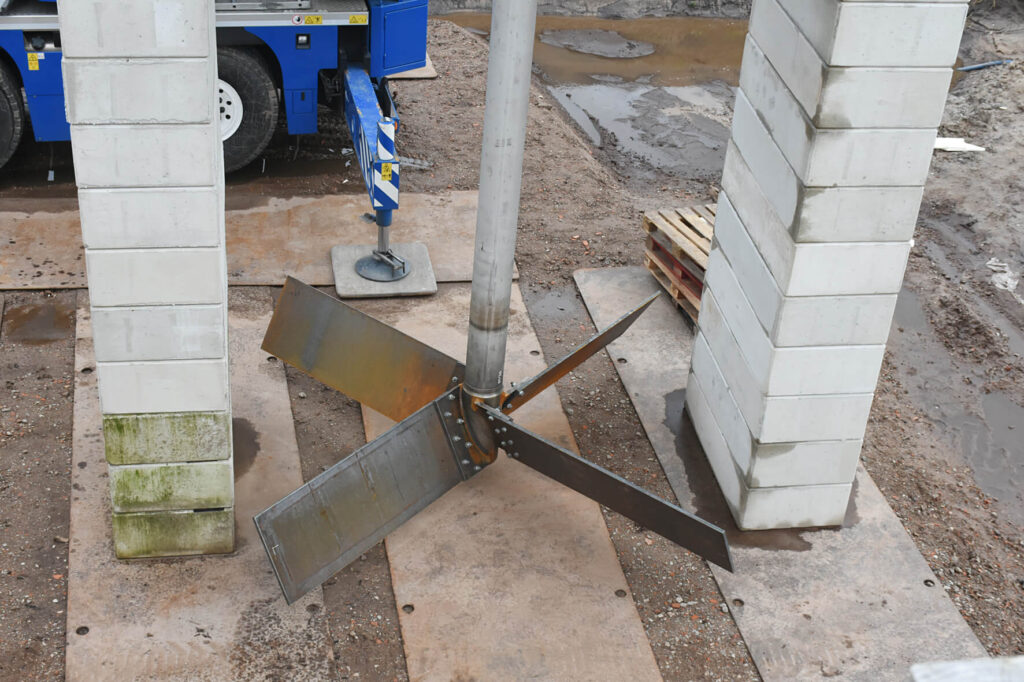
Jongia Mixing Technology and NORD
The Smits Group chose agitators from Jongia for the new plant. Pieter Smits: “We carried out an extensive market orientation for the required agitators, ultimately ending up with Jongia. They have a lot of experience in the industry. As our installation has an almost industrial character due to its size, that experience was of great importance to us.” Jongia, which is based in Leeuwarden, has been focusing on the development of mixing and stirring technology for the food processing, chemical and energy sectors since 1937 and is now the market leader in the Netherlands for biogas plants.
The drives
To drive the agitators in the new digester, Jongia chose MAXXDRIVE gearboxes from NORD. Area sales manager Bart Brouwer: “Our agitators require powerful gearboxes. NORD supplies MAXXDRIVE gearboxes that exactly meet our requirements. In addition, NORD is known for the quality of its products. We are therefore confident that the gearboxes will do what they were purchased for.” NORD’s MAXXDRIVE industrial gearboxes have a reduction ratio of 123:1, a power of 37 kW and an output torque of almost 29,000 Nm. Because of the application, the gearboxes meet all ATEX standards. The particularly powerful gearboxes are necessary in view of the large dimensions of the digester and its shape – rectangular instead of round – so that a lot of power is required to move the mass through the agitators.
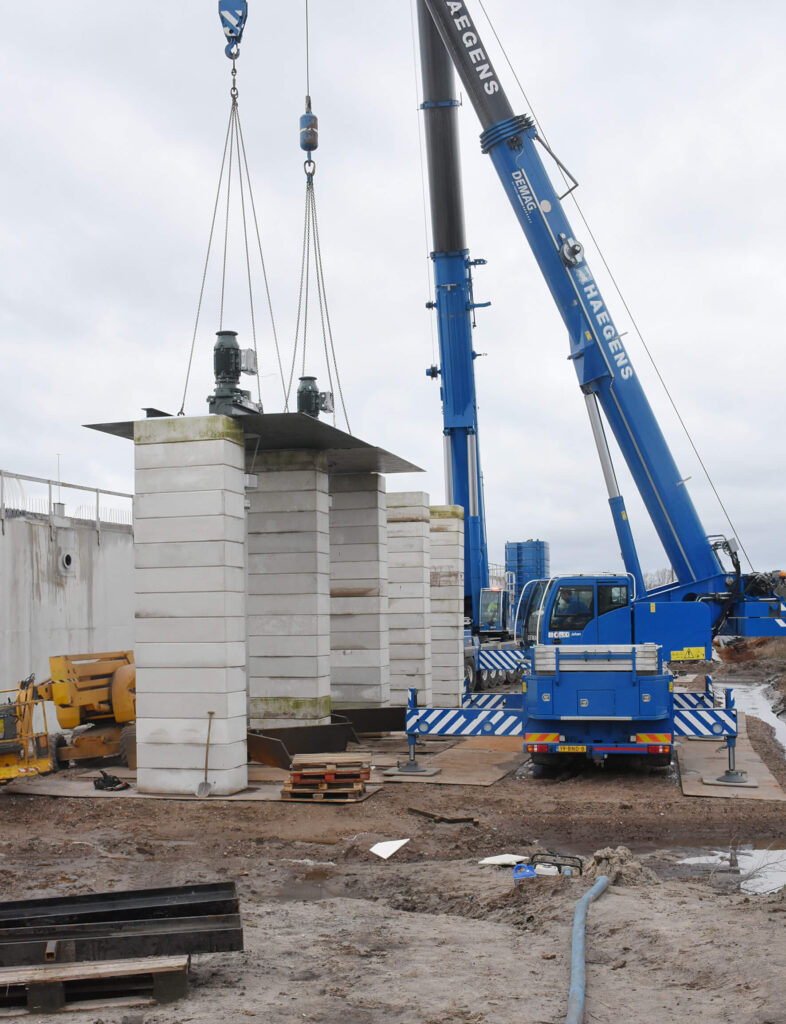
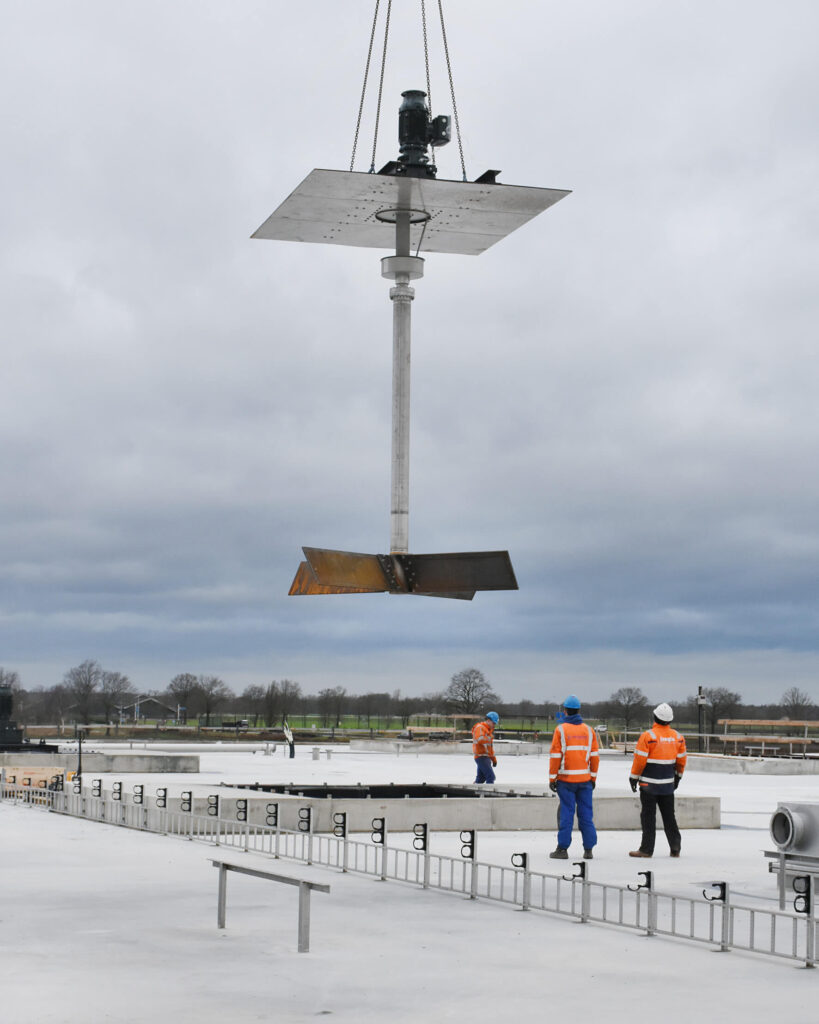
Rectangular
The new digester covers an area of about one hectare and consists of eight bunkers, each with two agitators on the roof. The methane released is collected at the top of the bunkers and delivered to the public gas network after cleaning and processing. Jongia’s mixers ensure that the materials to be digested form a stable and homogeneous mass in terms of temperature, viscosity and acidity, among other things, so that the microbes can do their work optimally and as much biogas as possible is produced.
The individual concrete digestion bunkers each have an area of 47.5 x 25.5 metres and are 5.5 metres high. Jongia’s sixteen agitators each consist of an approximately 4.5-metre-long shaft with four propellers at the bottom. The shaft is only fixed to the gearbox at the top and otherwise ‘floats’ freely in the fermentation mass. Bart Brouwer: “Digesters are usually round. This is not a problem with a rotating agitator. But these digesters have a different shape. In addition, there are several concrete columns in each digester that support the roof. This makes designing the right agitator a special challenge. We investigated this extensively and came up with a customised solution with two agitators per bunker. To validate our solution, we engaged an external company that did CFD modelling and flow profile and velocity analysis. This independent validation gives the Smits Group confirmation that the agitators and digesters do what is expected of them.”
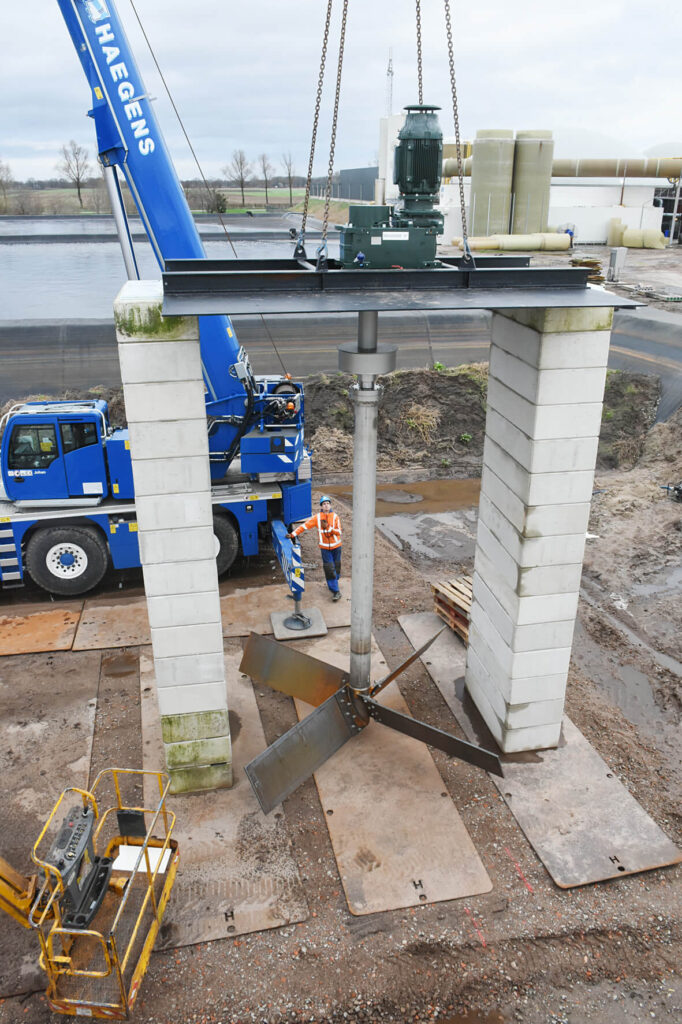
App or cloud
The agitators do not run continuously, but can be switched on and off as required and independently. The controls are located in a control cabinet, but can also be controlled remotely via a mobile app or even via the cloud. “Modern technology enables us to work extremely flexibly,” says Pieter Smits. “We can adjust production to the desired requirement at any time.”
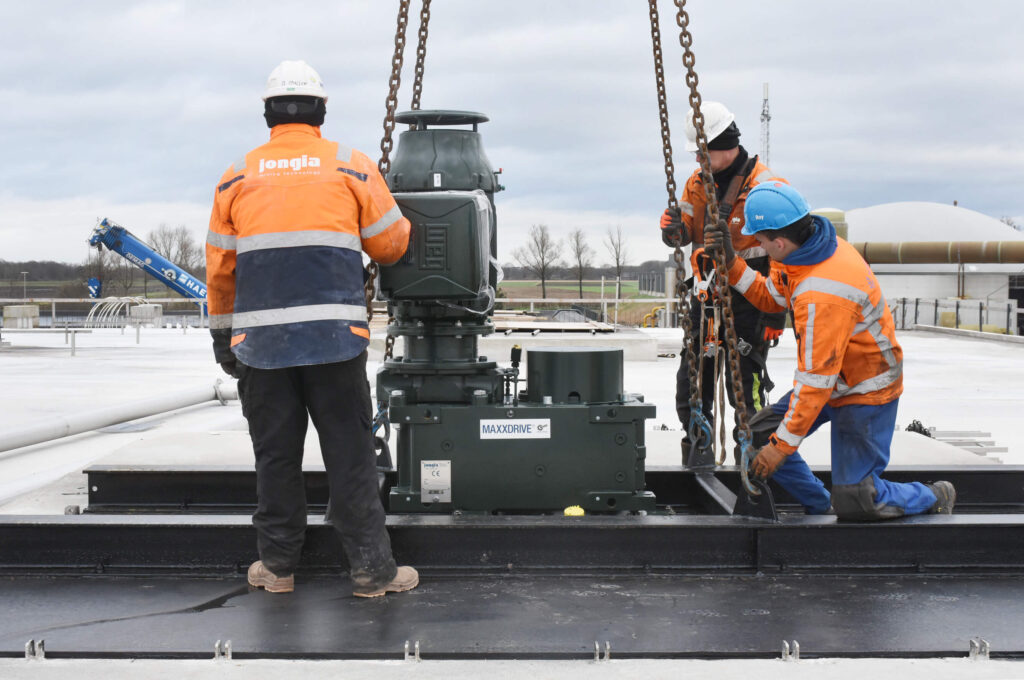
Future
The new agitators from Jongia with drives from NORD have been running since the end of 2023, and the Smits Group is satisfied with the results so far. Pieter Smits: “We want to add a second plant with another eight bunkers in the future. This will allow us to significantly increase our capacity and enable us to supply gas to 25,000 households. If you would like to know more about Jongia Biogas agitators, please take a closer look at: https://www.jongia.com/industries/bio-based-environmental/biogas/ Or contact: sales@jongia.comContact our specialized team for all your questions
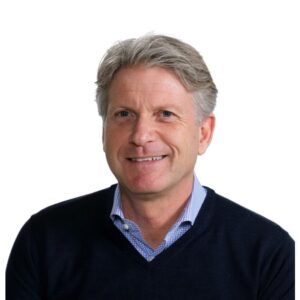
Tom Pruymboom
Sales Director
Area Worldwide
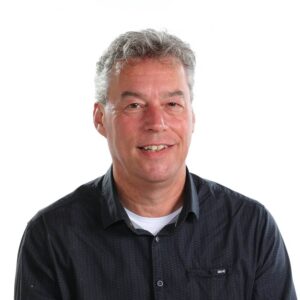
Bart Brouwer
Area Sales Manager
Area Worldwide
Related News
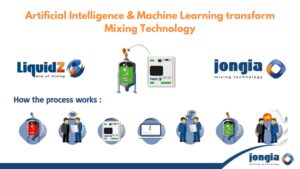
Artificial Intelligence and Machine Learning are Moving Up into Mixing Technology
In the ever-evolving landscape of industrial technology, artificial intelligence (AI) and machine learning (ML) are making significant strides in various sectors, including mixing technology. Jongia Mixing Technology is at the forefront of this revolution, integrating state-of-the-art sensor technology with advanced
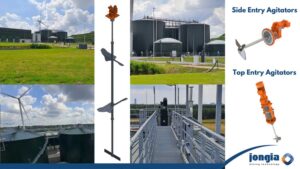
Jongia Mixing Technology‘s Biogas Production program
Optimizing Biogas Production with Jongia’s Innovative Technology Jongia is leading the way in improving biogas production with its advanced mixing solutions. In the biogas industry, effective mixing is key to maximizing energy output, minimizing power consumption and optimizing system efficiency.
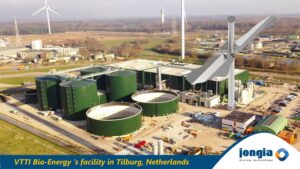
VVTI Biogas Tilburg
VTTI Biogas Tilburg is developing a new bio-energy facility, focusing on processing organic waste. The plant is expected to produce approximately 23 million cubic metres of biogas annually. A portion of this will be converted into green gas for the