Jongia Mixing Technology’s Redesigned Valves
Jongia Mixing Technology, an industry leader in valve innovation, has taken a significant step forward in the world of Ball Segment Valves. These valves are typically produced using either Stainless Steel or a specific variant of Hastelloy, known for their remarkable resistance to corrosion and wear.
Acknowledging the cost and labor-intensive nature of Hastelloy, Jongia Mixing Technology guided the exploration of corrosion-resistant and wear-resistant materials in the 3D production technology.
To enable Jongia to produce components in high alloy materials, Jongia has started a collaboration with Titomic. Titomic’s technology uses near-net shape additive manufacturing to replace complex welded assemblies with single-piece structures. More information can be found at: Revolutionising Additive Manufacturing: Titomic’s Structural Solutions
Under the Techno-G brand, Jongia Mixing Technology led the way in this cutting-edge initiative. Their research and development team undertook a mission to determine whether the components of a Ball Segment Valve could be manufactured using the 3D metal Cold spray process while still meeting the same material specifications as those used in conventional Ball Segment Valve production.
Extensive research and experimentation have been conducted on the 3D Cold spray printing process, utilizing Titanium as its core material. Jongia Mixing Technology, successfully redesigned the body of the Ball Segment Valve to ensure compatibility with the 3D Cold spray printing process.
Key benefits arising from the utilization of 3D printing technology:
- Reduced lead times
- Decreased raw material usage
- Enhanced design flexibility
- Lower production costs
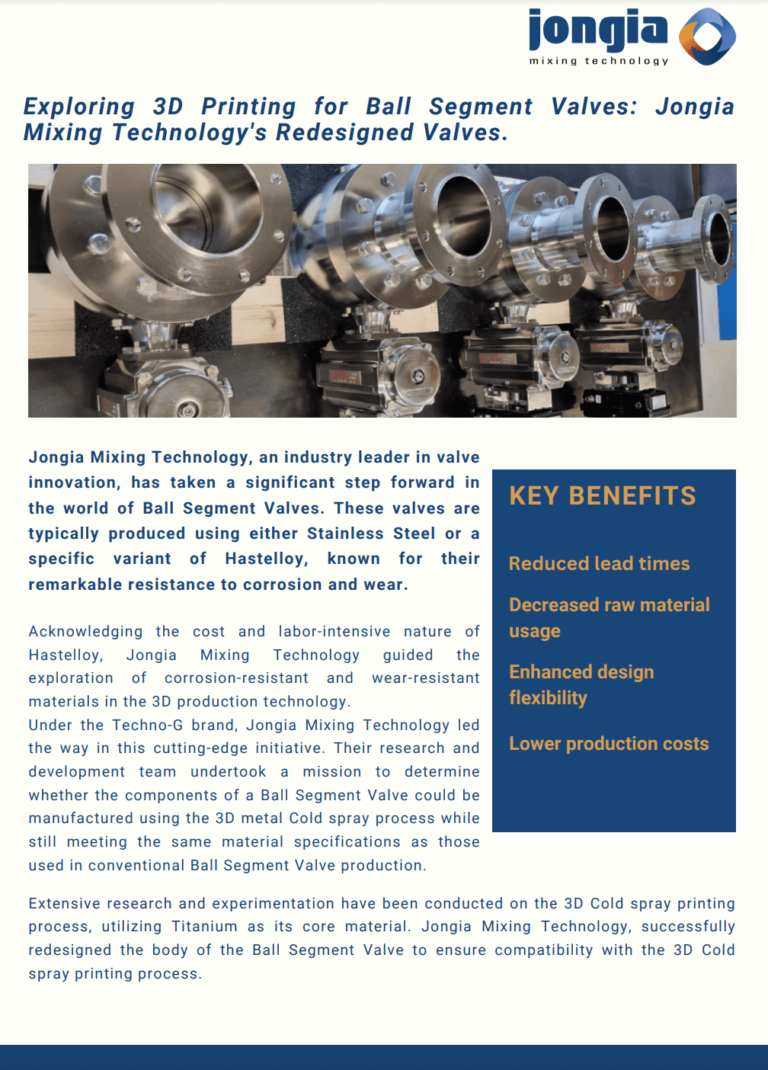
Download our free whitepaper
"Advancing 3D Printing: The Techno-G Ball Segment Valve"
Discover the full potential of the Techno-G Ball Segment Valve in our detailed whitepaper. Download now to explore how Jongia’s innovation can transform your processes.
Cold Spray 3D printing with a gas stream process
Cold spray 3D printing with a gas stream is an innovative additive manufacturing process that utilizes high-velocity gas to build 3D objects layer by layer. Unlike traditional 3D printing methods that rely on melting and solidifying material, this approach operates at relatively low temperatures.
Step by step approach:
- Material Selection: The process typically employs metal or metal alloy powders as the raw material. The choice of powder depends on the desired properties of the final object, such as strength, conductivity, or corrosion resistance.
- Gas Stream Propulsion: Instead of using high-velocity particles, this method employs a high-speed, often heated, gas stream, such as compressed air or nitrogen. The gas stream acts as the propellant for the metal powder.
- Material Deposition: The gas stream carries the selected metal powder and directs it onto the substrate or workpiece. As the particles make contact with the surface, they undergo plastic deformation and form strong metallurgical bonds with the underlying material.
- Layer-by-Layer Assembly: A computer-controlled system or robotic arm guides the gas stream nozzle to deposit the metal powder in a predefined pattern, building up the 3D object layer by layer.
- Cooling and Solidification: After each layer is deposited, the particles rapidly cool and solidify. Despite the term “cold spray,” this process generates some heat due to the high-speed impact, but it remains significantly cooler than traditional melting-based 3D printing methods.
- Repeated Process: Steps 4 through 6 are repeated until the entire 3D object is fully constructed. The precise control over the gas stream’s movement and material deposition pattern enables the creation of intricate and complex shapes.
The exploration of 3D printing through the Cold spray method is reshaping the landscape of valve production. This process promises remarkable advancements for the industry, placing cost-efficiency and design flexibility at the forefront. Watch this space for updates on this thrilling journey of innovation and transformation.
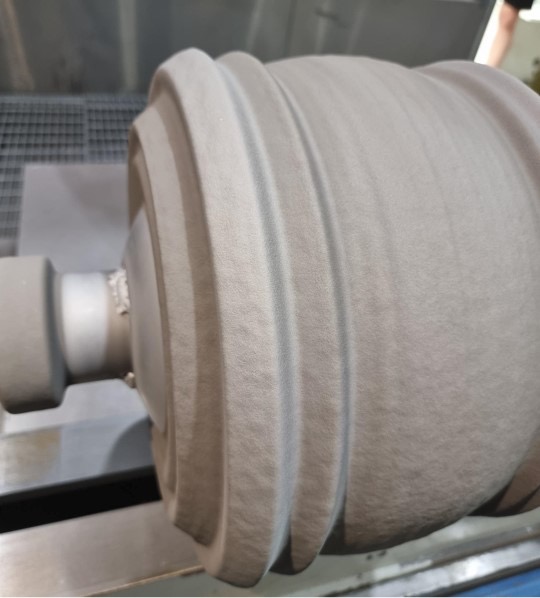
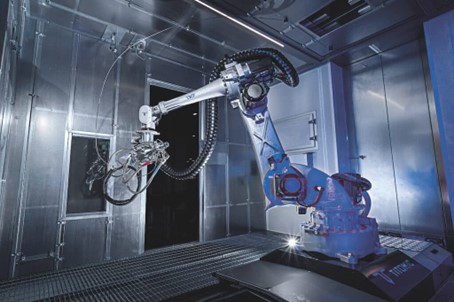
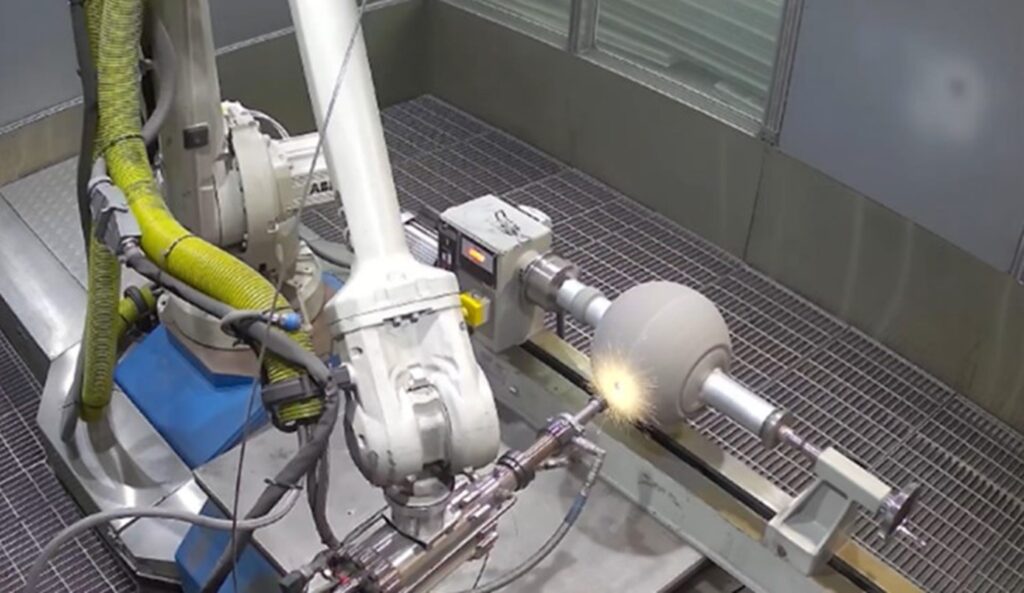
Related News
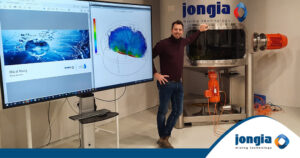
Innovative developments within agitator industry
To give insight into some of the developments within Jongia Mixing Technology, we would like to highlight what is currently going on in terms of innovative projects in which customization for our customers is key. For this article we spoke
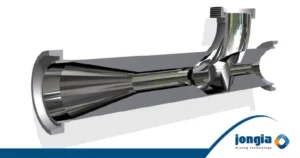
The Jet mixer: for efficiently dissolving of solids
Homogeneous dissolving of solids in liquids requires more than a tank with an agitator. For these mixing processes Jongia Mixing Technology supplies the so-called Jet mixer: an efficient powder dissolver. Operation and placement of the Jet mixer The Jet mixer