Usually Jongia is asked to mix liquids. But in this case Jongia got the opposite question by one of her customers in The Netherlands. In order to prepare lactose for further processing in the pharmaceutical industry, the customer was in search of an application to separate the lactose correctly. The process technique used for this is named “Crystallisation”. This is a technique that Jongia Mixing Technology has not only mastered but also optimised, as this case demonstrates.
These were the important preconditions in the crystallisation process that Jongia had to take into account:
- A large working area had to be created in order to optimise crystal growth.
- The product was not allowed to settle on the bottom.
- The crystals had to be the correct size, with the best quality.
- The heat transmission had to match the crystallisation process optimally
Creation of a large working area
As a large working area optimises crystal growth, Jongia chose to advise centrally mounted agitators with large blades.
Normally, the standard version agitator for crystallisation consists of a so-called “three-leaf clover”. However, Jongia did something “out of the box” and adapted the standard configuration by changing one of the blades to empower the influence on the flow. Due to this change the flow was more active, which not only increased crystal growth, but also made the product sink to the bottom less quickly.
Another element that Jongia added to the agitator setup is the use of a so-called rest stirrer. This rest stirrer is welded to the blades and ensures that no product is left on the bottom. As a result, right up to the last moment the entire tank content is included in the crystallisation process.
Validation by CFD/computer simulation
In order to prove the modifications suggested by Jongia would actually lead to a better result and the crystals would have the optimal size, Jongia used CFD/computer simulation.
Jongia also went a step further with the computer simulation by projecting the CFD simulation through the (double-walled) tank wall. This provided unique images, which allowed Jongia to validate the crystallisation process with the results from the CFD simulation and optimise the heat transmission to the stirring process. Eventually these results were sufficiently convincing that the customer purchased the agitators from Jongia.
An outstanding result for both the customer and Jongia.
Want to know more?
Would you like more information about the crystallisation process or the CFD/computer simulation?
Contact our specialized team for all your questions
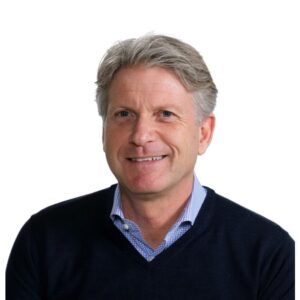
Tom Pruymboom
Sales Director
Area Worldwide
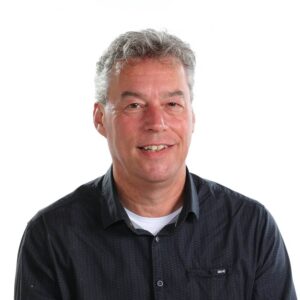
Bart Brouwer
Area Sales Manager
Area Worldwide
Technical Questions?
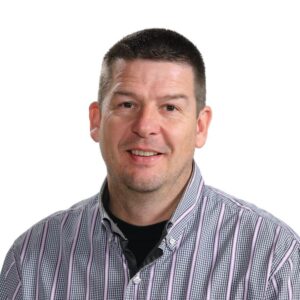
Sijko van der Veen
Application Engineer
Technical Specialist
Meet Jaap Grijpma
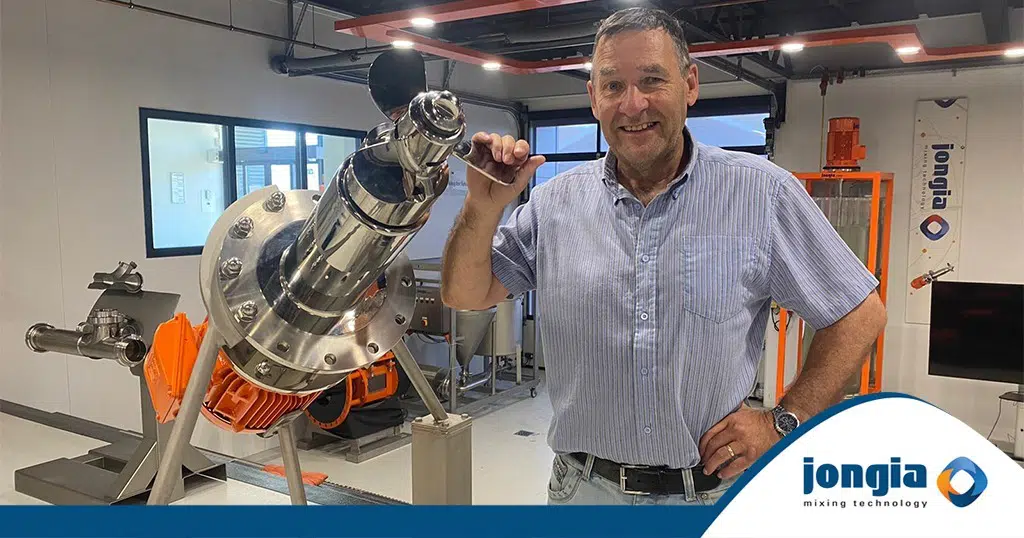
The face behind – Application Engineer Jaap Grijpma
Jongia Mixing Technology is more than an experienced and innovative supplier of mixing and stirring equipment. Behind the company name lies a large number of professional employees who dedicate themselves daily to customers and colleagues, with a passion for their
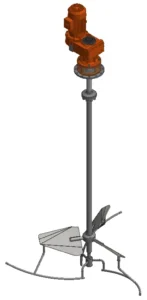
Excellent result by thinking outside the box
Usually Jongia is asked to mix liquids. But in this case Jongia got the opposite question by one of her customers in The Netherlands. In order to prepare lactose for further processing in the pharmaceutical industry, the customer was in