The sodium-ion battery (NIB or SIB) is a type of rechargeable battery that uses sodium ions (Na+) as its charge carriers. Its working principle and cell construction are almost identical with those of lithium-ion battery (LIB) types, but replace lithium with sodium.
Sodium-ion batteries are a potential alternative to lithium-based battery technologies, largely due to sodium’s lower cost and greater availability. Since SIBs use abundant and cheap materials, they are expected to be less expensive than LIBs. The environmental impacts of SIBs are also lower. Although SIBs are heavier and larger than LIBs, they are feasible for stationary energy storage systems where the weight and volume are less crucial.
SIBs received academic and commercial interest in the 2010s and 2020s, largely due to the uneven geographic distribution, high environmental impact and high cost of many of the materials required for lithium-ion batteries. Chief among these are lithium, cobalt, copper and nickel, which are not strictly required for many types of sodium-ion batteries. The largest advantage of sodium-ion batteries is the natural abundance of sodium. Challenges to adoption of SIBs include low energy density and insufficient charge-discharge cycles.
As of 2022, sodium-ion batteries had not become commercially significant, but this might change as the world’s biggest battery manufacturer, announced of starting mass production of SIBs in 2023. The technology is unmentioned in a United States Energy Information Administration report on battery storage technologies. Furthermore, no electric vehicles use sodium-ion batteries…yet.
History
Sodium-ion battery development took place in the 1970s and early 1980s. However, by the 1990s, lithium-ion batteries had more demonstrated commercial promise, causing interest in sodium-ion batteries to decline. In the early 2010s, sodium-ion batteries experienced a resurgence, driven largely by the increasing cost of lithium-ion battery raw materials.
Operating principle
SIB cells consist of a cathode based on a sodium containing material, an anode (not necessarily a sodium-based material) and a liquid electrolyte containing dissociated sodium salts in polar protic or aprotic solvents. During charging, sodium ions move from the cathode to the anode while electrons travel through the external circuit. During discharge, the reverse process occurs.
Materials (Anodes, Cathodes & Electrolyte)
Due to the physical and electrochemical properties of sodium, SIBs require other materials than those used for LIBs.
Anodes
SIBs use hard carbon, a disordered carbon material consisting of a non-graphitizable, non-crystalline and amorphous carbon. Hard carbon’s ability to absorb sodium was discovered in 2000. This anode was shown to deliver 300 mAh/g with a sloping potential profile above ⁓0.15 V vs Na/Na+. It accounts for roughly half of the capacity and a flat potential profile (a potential plateau) below ⁓0.15 V vs Na/Na+. Graphite anodes for LIBs offer typical capacities of 300–360 mAh/g. The first sodium-ion cell using hard carbon was demonstrated in 2003 and showed a 3.7 V average voltage during discharge. Hard carbon is preferred due to its excellent combination of capacity, (lower) working potentials and cycling stability.
Cathodes
Sodium-ion cathodes store sodium via intercalation. Owing to their high tap density, high operating potentials and high capacities, cathodes based on sodium transition metal oxides have received the greatest attention. To keep costs low, research attempts to minimize costly elements such as Co, Cr, Ni or V. A P2-type Na2/3Fe1/2Mn1/2O2 oxide from earth-abundant Fe and Mn resources can reversibly store 190 mAh/g at average discharge voltage of 2.75 V vs Na/Na+ utilising the Fe3+/4+ redox couple – on par or better than commercial lithium-ion cathodes such as LiFePO4 or LiMn2O4. However, its sodium deficient nature lowered energy density. Significant efforts were expended in developing Na-richer oxides. Copper-substituted Na0.67Ni0.3−xCuxMn0.7O2 cathode materials showed a high reversible capacity with better capacity retention. In contrast to the copper-free Na0.67Ni0.3−xCuxMn0.7O2 electrode, the as-prepared Cu-substituted cathodes deliver better sodium storage.
Research has also considered cathodes based on polyanions. Such cathodes offer lower tap density, lowering energy density on account of the bulky anion. This may be offset by the stronger covalent bonding of the polyanion that positively impacts cycle life and safety. Among polyanion-based cathodes, sodium vanadium phosphate and fluorophosphate have demonstrated excellent cycling stability and in the latter, an acceptably high capacity (⁓120 mAh/g) at high average discharge voltages (⁓3.6 V vs Na/Na+).
Electrolytes
Sodium-ion batteries can use liquid and non-liquid electrolytes. The limited electrochemical stability window of water results in lower voltages and limited energy densities. Non-liquid carbonate ester polar aprotic solvents extend the voltage range. These include ethylene carbonate, dimethyl carbonate, diethyl carbonate, and propylene carbonate. The most widely used non-liquid electrolyte uses sodium hexafluorophosphate as the salt dissolved in a mixture of these solvents. Additionally, electrolyte additives can improve performance metrics.
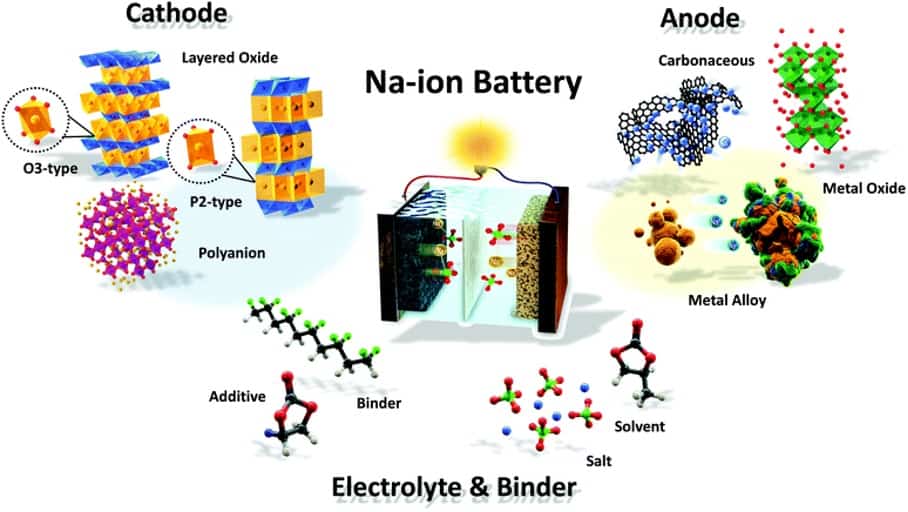
Comparison
Sodium-ion batteries have several advantages over competing battery technologies. Compared to lithium-ion batteries, sodium-ion batteries have somewhat lower cost, slightly lower energy density, better safety characteristics, and similar power delivery characteristics.
The table below compares how NIBs in general fare against the two established rechargeable battery technologies in the market currently: the lithium-ion battery and the rechargeable lead–acid battery.
Sodium-ion battery | Lithium-ion battery | Lead–acid battery | |
Cost per Kilowatt Hour of Capacity | $40–77 | $137 (average in 2020). | $100–300 |
Volumetric Energy Density | 250–375 W·h/L, based on prototypes | 200–683 W·h/L | 80–90 W·h/L |
75–165 W·h/kg, based on prototypes and product announcements | 120–260 W·h/kg | 35–40 Wh/kg | |
Cycles at 80% depth of discharge | Hundreds to thousands. | 3,500 | 900 |
Safety | Low risk for aqueous batteries, high risk for Na in carbon batteries | High risk | Moderate risk |
Materials | Earth-abundant | Scarce | Toxic |
Cycling Stability | High (negligible self-discharge) | High (negligible self-discharge) | Moderate (high self-discharge) |
Direct Current Round-Trip Efficiency | up to 92% | 85–95% | 70–90% |
Temperature Range | −20 °C to 60 °C | Acceptable:−20 °C to 60 °C. Optimal: 15 °C to 35 °C | −20 °C to 60 °C |
Jongia Mixing Technology is always able to assist in the guidance of the selection for the agitator configuration.
Just contact Jongia and ask for assistance.
We are always available for your mixer requests.
Contact us at: info@jongia.com or visit more Ion-Lithium battery related articles on our batteries page.
This article has been written by making use of certain information coming from the following websites:
Sodium-Ion Battery Wikipedia page
https://pubs.rsc.org/en/content/articlelanding/2017/cs/c6cs00776g
Contact our specialized team for all your questions
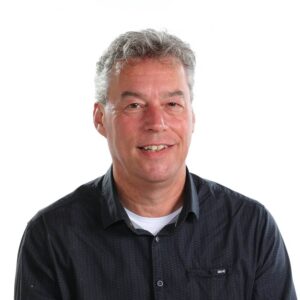
Bart Brouwer
Area Sales Manager
Area Worldwide
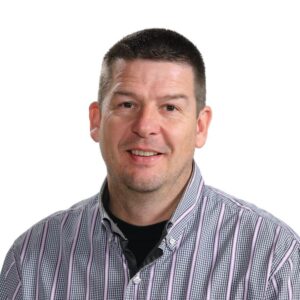
Sijko van der Veen
Application Engineer
Technical Specialist
Technical Questions?
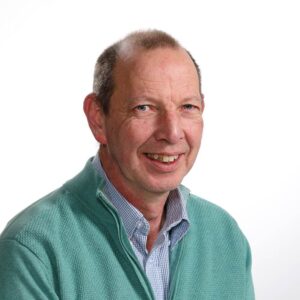
Jan Siert Tjeerdsma
Project Manager
Technical Specialist
Related Articles
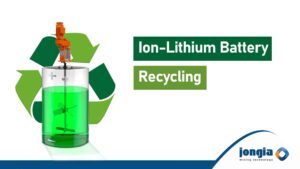
What is the recycling process for lithium
Current commercial lithium ion batteries mainly contain transition metal oxides or phosphates, aluminum, copper, graphite, organic electrolytes containing harmful lithium salts, and other chemicals. Therefore, the recycling and reuse of spent lithium ion batteries has been paid more and more
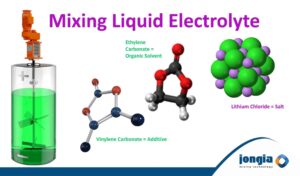
Mixing Electrolyte for Ion-Lithium Batteries
Electrolyte as basis for Ion-Lithium Batteries plays a key role in transporting the positive lithium ions between the cathode and anode, and consequently the charging and discharging performance of the battery. Hence, it needs to be checked for potential impurities.

Mixing the correct Ion-Lithium Battery Slurry is a real challenge!
Lithium-based battery technologies for electric vehicles use lithium-ions as the charge carrier. Depending on the application’s technical requirements, lithium is used with various chemistries such as graphite for the anode as well as nickel, manganese or cobalt oxides for the